Difference Between Static Balance and Dynamic Balancing
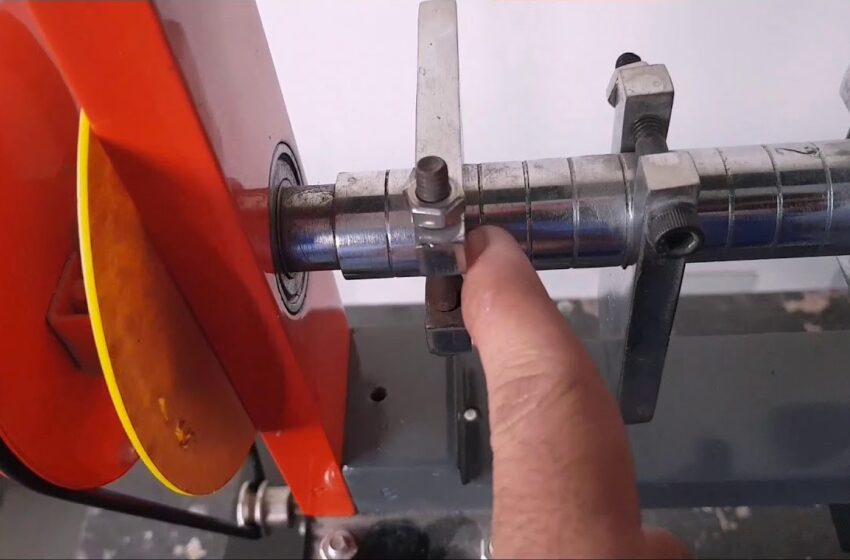
There are two types of balancing: Static balancing and dynamic balancing. What is the difference? Let’s know here.
Static Balancing
Static balancing is a process to determine the centre of gravity for a rotating shaft, gear or wheel. The main purpose is to determine if the component can be removed from its housing without falling over. Static balancing can also be used for determining the centre of gravity for an assembly containing several parts (such as a crankshaft) or when testing how well an assembly is balanced.
In order for a wheel to be balanced properly, the weight of all its components must be distributed evenly around its centre of gravity (CG). The CG is located on the axis of rotation (the centreline) and at equal distances from both sides of the wheel’s centreline. This means that if you have a wheel with an off-centre weight distribution, it will wobble back and forth as it rotates — this is known as “wobble.”
To understand why this happens, think about spinning a basketball on your finger; when you spin your finger slowly, the ball stays up there. But as soon as you speed up your spin, the ball starts wobbling because there isn’t enough centrifugal force to hold it in place as it moves faster. The same thing happens with wheels: If an off-centre weight distribution prevents them from spinning smoothly, then they’ll wobble instead.
Dynamic Balancing
Dynamic balancing is a process that balances rotating equipment at high speeds. Dynamic balancing ensures that all parts of a rotating component have equal vibration-damping characteristics under load, which minimizes vibrations and noise in high-speed machinery.
In Dynamic Balancing, the machine is driven by a motor and the system is not fixed on ground (like in Static Balancing). The dynamic balancing system is made up of a suspended platform that rotates to compensate for centrifugal force.
Dynamic Balancing is also known as Dynamic Balancing Machine or Dynamic Balancer. It uses a simple principle of centrifugal force to balance rotating parts. In this process, the rotating component is mounted on a suspended platform that spins freely in a horizontal plane. The components are then spun at high speed and the load is applied to the platform. Centrifugal force causes the component to move outwards from its axis of rotation leaving an imbalance on one side. As the platform rotates, centrifugal force acts upon the imbalance causing it to move back into equilibrium with the rest of the assembly.
This process continues until all components are balanced within permissible limits.
To know more on this topic, click here.